柔性印刷电路板(FPC)正成为消费电子、医疗设备及汽车电子的关键组件,而多层FPC凭借其高密度互连和三维布线能力,正在突破传统刚性板的设计限制。本文将深入探讨多层FPC设计的核心技术逻辑,结合工程实践案例,解析如何通过设计优化实现性能与可靠性的平衡。
一、多层FPC的核心设计挑战
1. 层间结构设计的“千层饼”难题
与刚性PCB不同,多层FPC需在柔性基材(如聚酰亚胺PI)上实现多层堆叠,典型结构包含:
屏蔽层:铜箔+电磁屏蔽膜(厚度≤12μm),抑制高频信号串扰;
绝缘层:低介电常数(Dk=3.2~3.5)的PI覆盖膜,控制阻抗波动;
导电层:压延铜(RA铜)或电解铜(ED铜),厚度1/3oz至2oz;
补强层:不锈钢或FR4,局部增强连接器区域的机械强度。
设计关键:需通过仿真软件(如ANSYS Mechanical)计算弯曲应力分布,避免层间剥离风险。例如,在折叠屏手机中,弯折区域的层数通常限制在6层以内,且采用“Staggered Via”(错位通孔)设计,分散应力集中点。
2. 高密度布线的“微缩手术”
线宽/线距:量产能力已突破25μm/25μm(激光直接成像LDI技术);
微孔工艺:机械钻孔极限0.1mm,激光钻孔可实现0.05mm微孔;
层间对位:X-ray检测确保±15μm对位精度,防止跨层短路。
典型案例:某智能手表主板采用8层FPC,在10mm×12mm区域内集成1200个连接点,通过“埋阻埋容”技术减少表面贴装元件数量。
二、四大设计优化方向
1. 电气性能:对抗信号衰减
阻抗控制:针对USB 3.2(5Gbps)等高速信号,采用差分对布线,误差控制在±10%;
串扰抑制:在相邻信号层间插入屏蔽层,并采用“Ground Via Fence”(接地孔阵列)隔离;
损耗补偿:选择低粗糙度铜箔(RTF铜,Rz≤2μm),高频段插损降低20%。
2.机械可靠性:动态弯曲设计
弯曲半径:动态弯曲场景(如机器人关节)需满足R≥1.5t(t为总厚度),静态弯曲场景R≥0.5t;
材料匹配:铜层延展率需>15%(ASTM E8标准),避免弯折时断裂;
应力缓冲:在弯折区域采用“波浪形走线”或“S形走线”,提升疲劳寿命至10万次以上。
3. 热管理:柔性电路的“散热悖论”
导热路径设计:在LED灯带等大电流场景,通过铜层开窗+导热胶填充,热阻降低至1.5℃/W;
耐温材料:选择高Tg基材(Tg≥200℃),防止高温分层;
热膨胀系数(CTE)匹配:铜(17ppm/℃)与PI(40ppm/℃)的CTE差异需通过层压工艺补偿。
4. 可制造性设计(DFM):从图纸到量产
拼板设计:采用“邮票孔+加强筋”组合,平衡柔性与生产效率;
覆盖膜开窗:激光切割精度±25μm,避免焊盘污染;
测试点布局:预留4-wire Kelvin测试点,确保阻抗测试准确性。
二、行业痛点与创新解决方案
1. 层间错位:引入“光学靶标对齐系统”
在10层以上FPC制造中,通过CCD相机捕捉每层的对位标记(Alignment Mark),实时调整压合参数,将层偏从±50μm压缩至±20μm。
2. 焊接失效:开发“柔性-刚性混合设计”
在汽车雷达FPC模块中,将BGA焊盘区域设计为刚性FR4补强结构(厚度0.8mm),焊点抗剪切力提升至35N,通过TM-650 2.4.8标准测试。
3. 成本控制:推行“模块化设计”
某医疗内窥镜厂商将12层FPC拆分为“3个4层子模块+柔性跳线”,良率从65%提升至88%,成本下降30%。
四、选型指南:如何评估多层FPC设计能力?
层间绝缘可靠性:能否通过IPC-TM-650 2.6.16湿热循环测试(85℃/85%RH,1000小时)?
动态弯曲寿命:是否具备双轴弯折测试设备(如RDC-01)及数据报告?
信号完整性验证:是否提供HyperLynx或Sigrity仿真报告?
特殊工艺储备:如异形镂空设计、立体3D贴合技术等。
五、前沿技术趋势
嵌入式元件:在FPC内部埋入电阻/电容,减少表贴元件数量(日本旗胜已量产);
透明FPC:采用ITO(氧化铟锡)导电层,透光率>85%,用于AR眼镜光机模组;
生物可降解FPC:基于PLA(聚乳酸)基材,满足医疗植入设备的环保需求。
总结

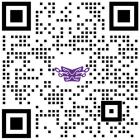